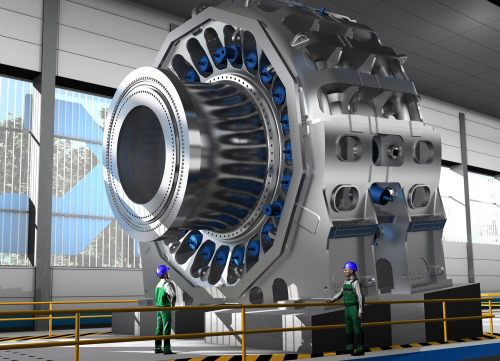
Impresionante edificio de testeo de rodamientos por SKF
Where do you test some of the biggest bearings on earth?
Colossal. Gargantuan. Humongous. Just some of the words you might use to describe these types of bearings. We’re talking bearings that would by any comparison dwarf most cars. Bearings used in, for example, the wind power industry. Bearings so large that when it comes to testing these behemoths, specialized infrastructure is the only way to cope with the sheer size of them.
To better cater for the development of these large bearings, the world’s highest-performance test centre is currently under construction. The ground-breaking ceremony officially unveiled the project on the 14th July, in front of a complex that covers over 3,000 square metres – truly one of a kind.
The complex is situated in the Germany town of Schweinfurt. If you’ve heard the name, you might already know that the town has a history intertwined with large bearing production.
Since 1990 it has been quietly establishing itself as the place to go when large bearings are needed. What this means is that it already has the infrastructure needed to support the creation of a new testing facility – everything in terms of product manufacturing technology (for materials and large bearing transport within the factory) as well as packaging and shipping logistics are already established.
Add into the mix the new high-performance testing facility, and Schweinfurt now boasts the full spectrum of capability when it comes to delivering on large-bearing requirements.
The new test centre will have two LSB test rigs; one for testing bearings used in wind turbine main shafts and one for applications across a wider scope of industries; these include marine, mining, construction and steel. The benefits of this are many. Product dynamics, maximum power, bending moment and rotational speeds – all will be now outperforming every other existing testing station, thanks to the new testing facility.
It is one of a kind and the largest ever. We estimate that the findings from the “smaller” of the two new test stations alone will contribute to reducing CO2 emissions by thousands of tonnes per year. But in order to achieve the required findings, the new testing station must unleash huge amounts of power. This power must, however, be directed into the right channels, and this is why both new test facilities must be placed on insulated foundations. The largest of these weighs several thousand tonnes.
Another huge benefit is ‘more realistic’ testing, which contributes to drastic reductions in energy and material use, especially in the production of future generations of large bearings. In addition, the test centre will optimize the efficiency of renewable energy sector technologies. This ability to develop large bearings much more accurately (according to their individual applications) will in the future mean greater durability and reliability.
The monetary investment has been high, but equally a lot of knowledge investment has been poured in, to make sure it’s a success. And with good reason, creating the highest performance test centre for large bearings in the world is no mean feat. The new testing station will also shed light on completely new areas – information and prognoses that before now, were simply not possible, will now be able to be explored and taken advantage of for future large bearing development.
For further reading on the new testing facility, take a look at the Press Release: http://bit.ly/1M7Qh4n